
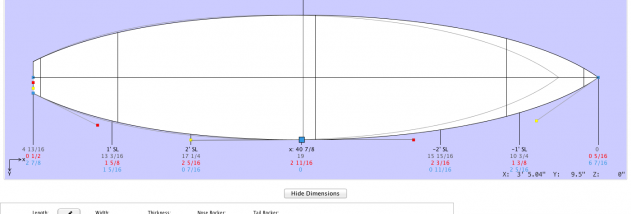
#Aku shaper software full
The board is now ready for the full laminating or ‘glassing’ process using fibreglass cloth and epoxy resin. This is done in sections using a hot cutting wire machine as shown in the below images. Stage 1 – Cutting the *EPS or **PU Blanksīefore any Circle One board can be shaped, the ‘blank’ (or rectangular chunk of EPS or PU foam) needs to be cut. So, there is still plenty of fine craftsmanship that goes into the finishing of each and every board. Machine assisted shaping allows us to create precision shapes and improve production levels, but the skills required to finish, refine and laminate (glass) a board is still where the majority of the work lies.
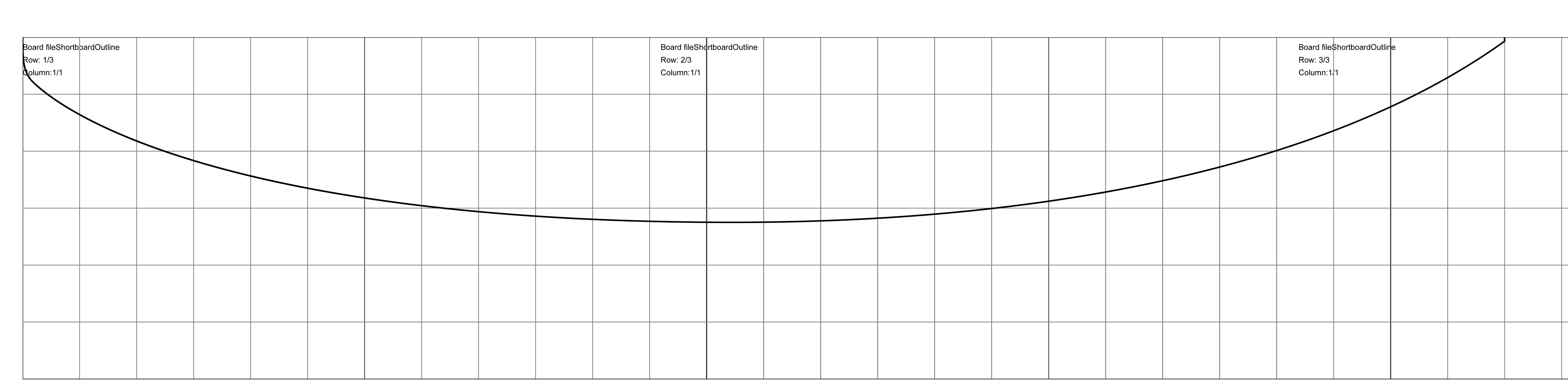
Put a Circle One board next to another and they may look similar but how do you really know what’s underneath? Or if the board was shaped by someone with over 40 years experience? The term “Hand Finished” or “Hand Crafted” applies to all of our board making process. Whichever board you choose, a credible seller should know exactly what materials a board is made from (for example, what type of glassfibre is used, Porcher or generic Chinese glass?, where does the Epoxy resin come from?) We only use premium Porcher E-glassfibre because there is a world of difference between that and cheaper glassfibre and it makes a massive difference to the durability and longevity of the board. They are made from foam, fibreglass and resin which means we produce a product superior in durability and strength to weight ratio. Boards produced in this way are typically much heavier and lack any true performance characteristics. The term ‘pop-out’ actually refers to the cheapest way to make a surfboard which involves making the hard outer layer of a board (usually a plastic composite) from a mold and then filling it with expandable foam. The use of CAD programs such as AKU and CNC machine is often (wrongly) associated with ‘pop-out’ boards. It is designed to help shapers keep their direct relationship with surfers and protect surfing from the loss of personalisation we’ve seen in other sports.” “The AKUshaper system was created to preserve the art of the custom surfboard. We believe all boards are precision instruments and should excel in function: that is why we have invested in the benefits of the AKU system. The move to machine shaping allows for efficient production and more time spent on the actual design and development of Circle One board shapes. Circle One have invested in two CNC machines installed by Mike Rickard, Director at AKU Shaper.
#Aku shaper software software
The software produces a ‘file’ for each shape which is programmed into a state-of-the-art AKU Shaper CNC (Computer Numercial Control) machine which shapes the surfboard from a block of EPS foam using a circular cutter. The AKU software allows sub-millimetre accuracy to be achieved representing a revelation for creativity and experimentation. These days, the process of achieving shaping excellence is transformed by the use of industry-renowned CAD software ‘AKU Shaper’, which enables Jeff to ‘shape’ boards using a 3D software interface. As demand grew, Jeff worked around the clock to shape all boards to his own exacting standards. In the early days, Jeff Townsley, Circle One founder and shaper shaped all boards from scratch by hand. Read more about the Circle One story here or read on to learn more about our fascinating Epoxy Surfboard manufacturing process.
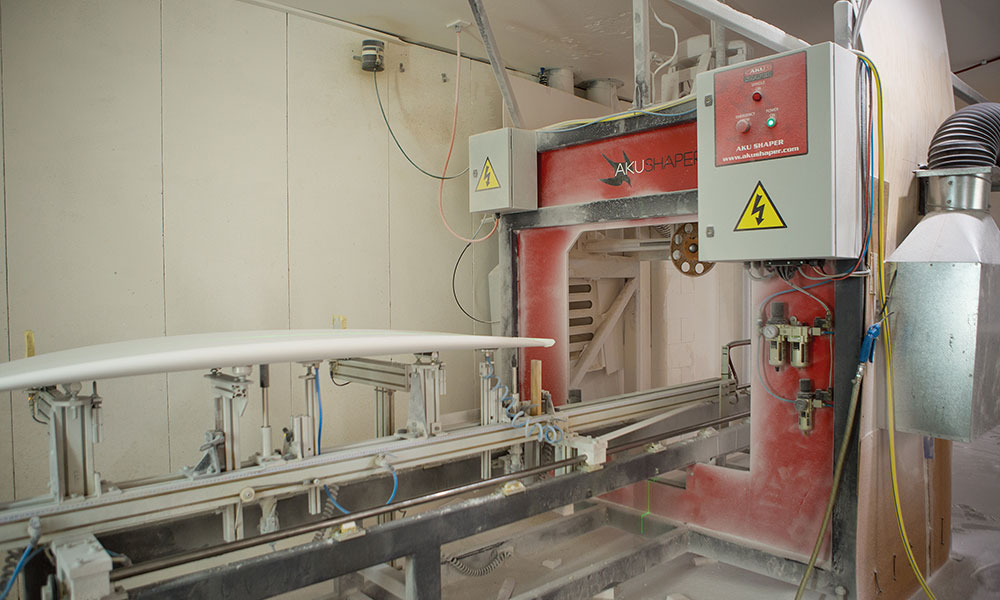
You can be sure when you purchase a Circle One product you are investing in years of manufacturing expertise and heritage.
#Aku shaper software pro
All Circle One products are precision-cut and hand crafted to exacting standards using only the best materials such as superior strength Porcher E-Fibreglass in our Surfboards, Hi-Tensile 6oz Carbon Fibre in our Carbon Pro Surfboard and Carbon Skimboard ranges and Super-stretch grade neoprene in our Wetsuit and Neoprene Accessories. We know that our reputation is only as good as the last Board, Wetsuit or Accessory we produce which is why we employ a team on the front-line to quality check production and maintain a no-compromise commitment to manufacturing excellence. CENTRE BUOYANCY AIDS & SPRAY JACKET/KAGĪt Circle One we’re passionate about riding the wave of innovation, developing and designing all our products in the UK and manufacturing in the Far East.
